Jobb anyagkihozatal a fenntarthatóságért!
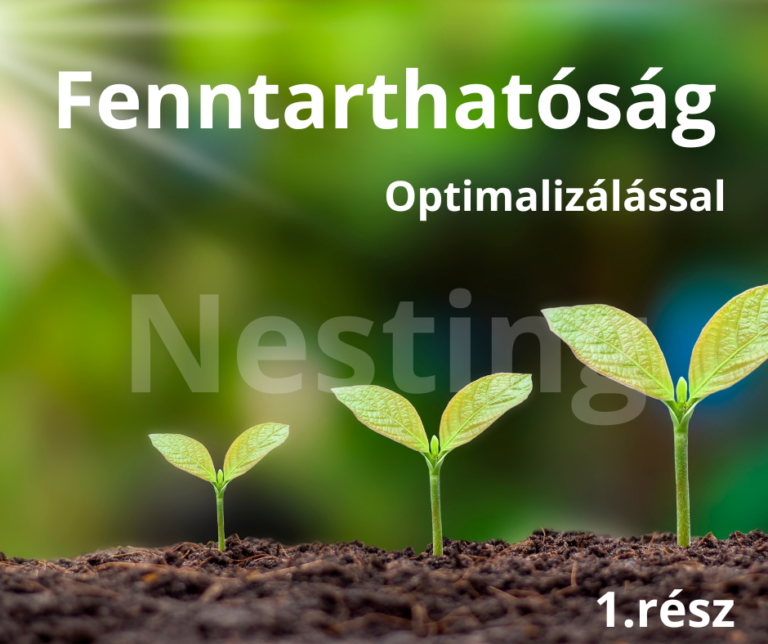
A régi dogmák még működnek?
A magyar kis- és középvállalkozások (KKV-k) napjainkban rendkívül nehéz gazdasági környezetben működnek. Az egyre növekvő árverseny, a csökkenő rendelések és a szűkülő határidők hatalmas nyomást helyeznek a vállalkozásokra. A piac jelentős része továbbra is régi, megszokott munkafolyamatokat és szoftvereket használ, amelyek már nem felelnek meg a modern ipari kihívásoknak.
A termelési hatékonyság kulcsfontosságú tényezővé vált a versenyelőny megtartásában. Azok a vállalatok, amelyek képesek a rendelkezésre álló erőforrásaikat optimalizálni, jelentős költségmegtakarítást érhetnek el. Az egyik ilyen kulcsfontosságú tényező az anyagkihozatal javítása, amely akár egyetlen szoftverfrissítéssel is elérhető.
Ebben a blogbejegyzésben bemutatom, hogy egy modern, fejlett gyártáselőkészítő szoftver hogyan segíthet a jobb táblatervek létrehozásában, ezáltal jobb anyagkihozatalt biztosítva, ami nemcsak a költségeket csökkenti, hanem a környezeti terhelést is mérsékli.
A hagyományos munkafolyamatok korlátai
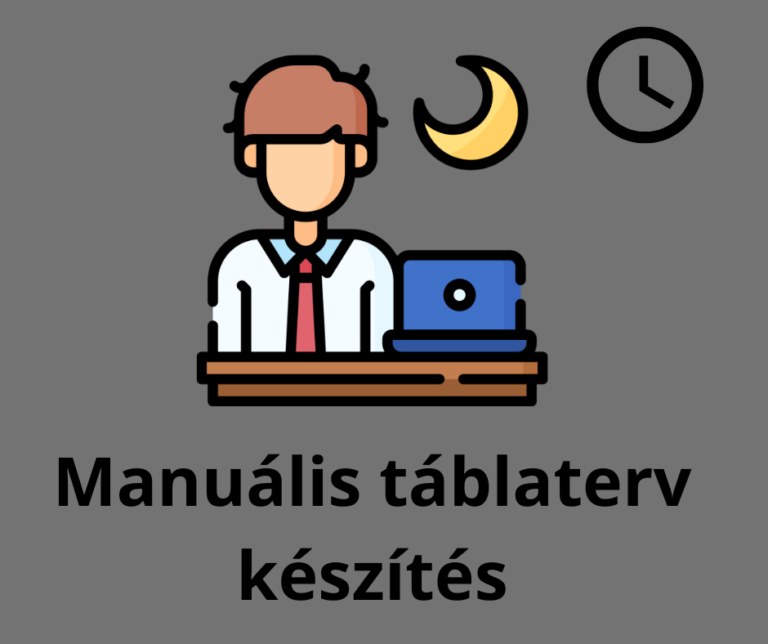
A magyarországi lemezmegmunkáló vállalkozások többsége azokat a szoftvereket használja, amelyet többnyire az első lézervágó vagy stancoló gépe mellé vásárolt. Ezen szoftverekre építették ki a munkafolyamatokat, amelyek igazából idővel a fejlődés elsődleges gátjai lettek. Minden bizonnyal mindannyian ismerjük ennek az okát: A megszokás. A szokások azért ragadnak ránk, mert megkönnyítik az életet – kevesebbet kell gondolkodni, minden megy rutinból. Váltani nehéz, mert az agyunk szereti a megszokott dolgokat. Egy új szokás kialakítása kb. 21-66 nap, de kitartás, ismétlés és motiváció kell hozzá.A komfortzóna elhagyása nélkülözhetetlen a fejlődéshez és a hatékonyabb munkamódszerek bevezetéséhez.
A régi szoftverek legnagyobb hátránya, hogy hiányzik belőlük az automatizmus. A korábbi szerényebb erőforrásokra készült alkalmazások egyszerűen technológiailag nem volt képes olyan táblaterveket előállítani, amelyeknek a hulladékaránya a lehető legalacsonyabb. Különösen igaz ez ha sokféle alkatrésszel kell egyszerre dolgozni (mondjuk 100 féle alkatrész egy csomagban).
A korábbi berögződések szerint egy algoritmus soha nem képes úgy gondolkodni mint egy ember. Ez részben igaz is, hisz a legtöbb fejlett nesting algoritmus máshogy gondolkodik mint egy ember, legfőképpen sokkal gyorsabban. Emiatt azonos időkeretben gondolkodva (legyen mondjuk 20 másodperc) egy ember soha nem lesz képes olyan minőségű terveket létrehozni. Amit érdemes elfogadnunk, hogy ez nem ellenünk szól, hanem minket segít. Ha valaki korábban egy bonyolult csomaggal órákat eltöltött mire a legjobb szabásterv előállt, annak most ez nagy segítség, hogy ez manapság percek alatt lehetséges és minden bizonnyal jobb hulladékarányt érünk el.
Nem beszélve arról, hogy az eltérő tapasztalati szinttel rendelkező munkatársak miatt az egyes táblatervek optimalizáltsága változó lehet. Ha ezek mellé hozzá vesszük, hogy a megspórolt táblák mellet mind a programozásban mind pedig a gyártásban is (kevesebb anyagmozgatási idő pl) jelentős időkent tudunk megtakarítani.
A korábbi 15-20 éves szoftverekkel összehasonlítva átlagosan 8%-os hulladékarány javulás tapasztalható. A megtakarított összeg igen jelentős lehet és pusztán csak egy régi szokásunkat kell hozzá elhagynunk.
Hogyan gyorsíthatod fel a gyártáselőkészítést modern szoftverekkel?
Először is érdemes szétnézni a piacon, hogy milyen szoftveres megoldások elérhetőek. A legtöbb új generációs szoftver már 64 bites alapokon nyugszik, emiatt több erőforrást tud felhasználni a számítási műveletekhez. Ezt azért érdemes előzetesen tesztelni. A legtöbb új algoritmus hozza a 8%-os hulladékarány javulást.
Némelyik képes direkt ERP kapcsolatra, ezek álltalában valamilyen fájl interfészek (XML adatcsere), de vannak már API (Application Programming Interface) -n keresztül is kommunikálni képes szoftverek a piacon. Az automatikus adat import/export mellet álltalában rendelkezésre állnak a kézi tömeges adatfeltöltések is mint például egy Excel fájl vagy egy CSV fájl betöltése. Minden esetben legyen szó akár kézi vagy automatizált feltöltésről, létezik egy specifikáció, ami leírja, hogy milyen formátumban kell az adatot biztosítani. Erre érdemes odafigyelni, valamint arra, hogy biztosítanak-e szakmai támogatást az interfész fejlesztéséhez.
Természetesen a legnagyobb előny akkor érhető el, ha az alap adatokat nem nekünk kell felvinnünk. Még ha a legminimálisabban is töltjük ki az adatokat (mit akarunk kivágni, milyen darabszámban, milyen anyagminőségben és esetleg melyik ügyfelünké a projekt) akkor is akár 1-2 percet is eltölthetünk egy alkatrésszel. A valóságban általában több adatot adnak meg a cégek vagy maga az adatminőség rossz (rajzból, e-mailből kell az információkat kikeresni).
Az már egy külön történet, hogy maga a forrásfájlok is a legtöbb esetben hibásak, hiányosak, így sok idő szükséges a javításukra. Tehát nem mindegy, hogy milyen szoftverrel dolgozzuk fel őket. Olyannal, ami a kezünk alá dolgozik és egy sor automatizmussal javítja a hibák többségét vagy egy olyan szoftverrel dolgozunk tovább, amiben továbbra is nekünk kell minden egyes apró hibát kijavítunk.
Egy jól megválasztott szoftverrel sokat nyerhet a vállalkozásunk. Érdemes hát a kiválasztásra kellő időt szánni.
Példa egy KKV anyagkihozatal javítására
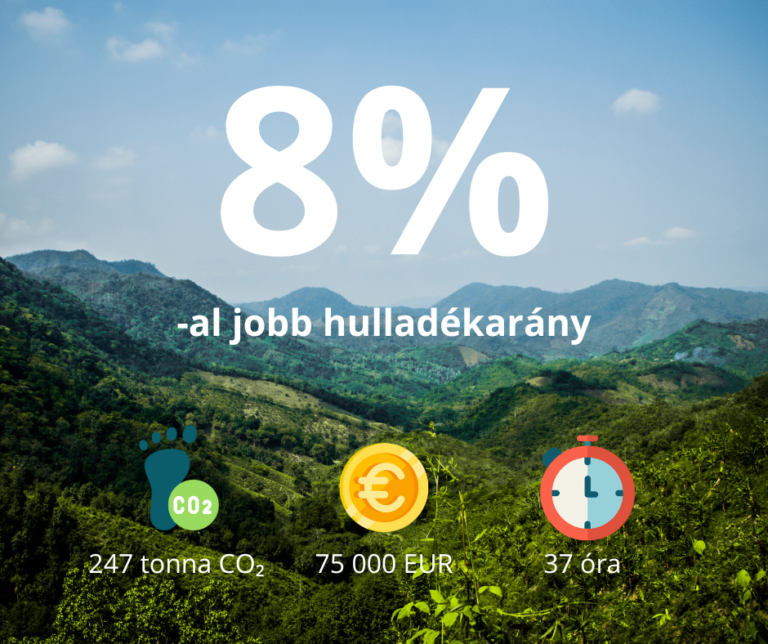
Tegyük fel, hogy egy lemezmegunkáló kisvállalkozás évente 1000 tonna alapanyagot használ fel, amelynek kihozatala jelenleg 65%. Az anyagarány a következőképpen alakul:
Szénacél: 80%
Rozsdamentes acél: 15%
Egyéb fémek (alumínium, sárgaréz): 5%
Anyagárak tekintetében szénacél esetében egy 600 €/tonna míg rozsdamentes acél esetében 2 000 €/tonna valamint egyéb fémek esetében 2 500 és 4 000 €/tonna átlagárat vettem alapúl (alu és sárgaréz esetében).
Jelenlegi 65%-os kihozatal:
Hasznosított anyagmennyiség: 1000 tonna × 65% = 650 tonna
Anyagmennyiség összetétel szerint:
- Szénacél: 650 tonna × 80% = 520 tonna
- Rozsdamentes acél: 650 tonna × 15% = 97,5 tonna
- Egyéb fémek: 650 tonna × 5% = 32,5 tonna
- Alumínium: 32,5 tonna × 60% = 19,5 tonna
- Sárgaréz: 32,5 tonna × 40% = 13 tonna
Anyagköltség jelenleg:
- Szénacél: 520 tonna × 600 €/tonna = 312 000 €
- Rozsdamentes acél: 97,5 tonna × 2000 €/tonna = 195 000 €
- Alumínium: 19,5 tonna × 2500 €/tonna = 48 750 €
- Sárgaréz: 13 tonna × 4000 €/tonna = 52 000 €
Összesen: 312 000 € + 195 000 € + 48 750 € + 52 000 € = 607 750 €
Javított 73%-os kihozatal (tehát +8%):
Hasznosított anyagmennyiség: 1000 tonna × 73% = 730 tonna
Anyagmennyiség összetétel szerint:
- Szénacél: 730 tonna × 80% = 584 tonna
- Rozsdamentes acél: 730 tonna × 15% = 109,5 tonna
- Egyéb fémek: 730 tonna × 5% = 36,5 tonna
- Alumínium: 36,5 tonna × 60% = 21,9 tonna
- Sárgaréz: 36,5 tonna × 40% = 14,6 tonna
Anyagköltség optimalizációt követően:
- Szénacél: 584 tonna × 600 €/tonna = 350 400 €
- Rozsdamentes acél: 109,5 tonna × 2000 €/tonna = 219 000 €
- Alumínium: 21,9 tonna × 2500 €/tonna = 54 750 €
- Sárgaréz: 14,6 tonna × 4000 €/tonna = 58 400 €
Összesen: 350 400 € + 219 000 € + 54 750 € + 58 400 € = 682 550 €
Egy fejletebb táblaterv készítő szoftver segítségével a kihozatal átlagosan akár 8%-kal növelhető, vagyis 65%-ról akár 73%-ra is nőhet. Ez azt jelenti, hogy a vágott anyagmennyiség 650 tonnáról 730 tonnára nőhet, ugyanannyi éves alapanyag felhasználást feltételezve.
A kihozatal 8%-os javulása éves szinten körülbelül 74 800 € anyagköltség-megtakarítást eredményezhet.
CO₂ kibocsátás csökkentése
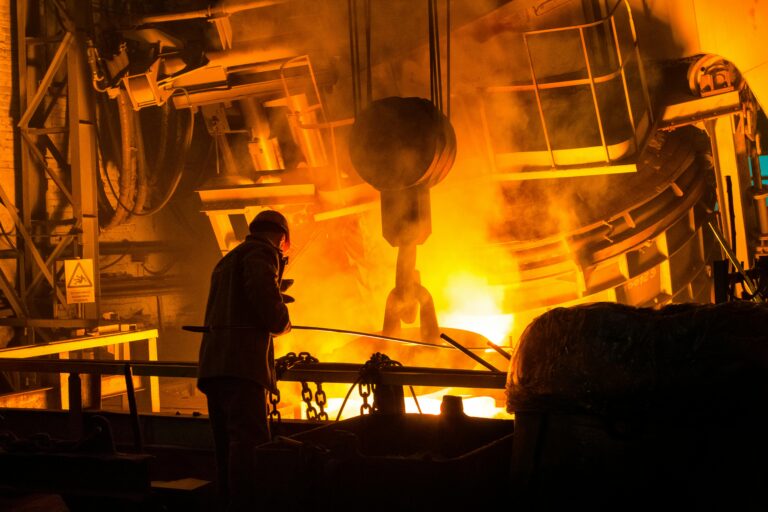
Az acélgyártás egyik legnagyobb környezeti hatása az alapanyag előállításához és annak megmunkálásához kapcsolódó szén-dioxid-kibocsátás. A jobb anyagkihozatalnak köszönhetően:
Kevesebb nyersanyagra van szükség → csökken az acélgyártásból származó CO₂ kibocsátás.
Jobb kihasználtsággal üzemelnek a gépek → csökken a lézervágó gépek energiafelhasználása.
Egy 6 kW-os Fiber lézervágó gép a fenti anyagmixet figyelembe véve 58,73 kWh/tonna energiaigénnyel működik. Könnyen bele lehet esni abba a hibába, hogy a jobb kihasználtság révén kevesebb alapanyag vágására lenne szükség, de ez nem igaz. A vágandó kontúr azonos marad, viszont a mellékidőkből sokat lehe lefaragni. Egy palettaváltás átlagosan 30-60 másodperc között mozog, míg egy lemeztábla fel illetve lerakása a vágóasztalra szintén időigényes. Ennek mértéke nagyban függ az adott kezelő ügyességétől valamint a helyi adottságoktól, de álltalánosságban elmondható, hogy 2-5 perc között van egy felvétel és egy lerakás. A táblánként akár 5-10 perc időnyereség hosszú távon biztosan hatással van az energia felhasználásunkra is.
Az acél és a színesfémek előállítása jelentős környezeti terheléssel jár, ezt aligha kell részletezni. Természetesen vannak kezdeményezések a CO₂-kibocsátás csökkentésére, például a zöld acélgyártás, amelyről Maróti Ádám egy remek cikket írt a Holdblogon.
Az interneten elérhető adatok alapján igyekeztem egy átlagértéket felvenni a különféle nyersanyagok előállításával kapcsolatban. Szénacél esetében 2,2 t CO2/tonna míg rozsdamentes acél esetén 5,5 t CO2/tonna. Színesfémek esetében (alu,réz) egy átlag 9,0 t CO2/tonna vettem alapul.
Ha ez előző bekezdésben lévő anyagmennyiségeket felszorozzuk ezekkel az értékekkel, akkor megkapjuk, hogy 80 tonnával jobb anyagkihasználás esetén kb. 247 tonna CO₂/év csökkenést érhetünk el.
Összegzés: Miért éri meg fejlettebb gyártáselőkészítő szoftverre váltani?
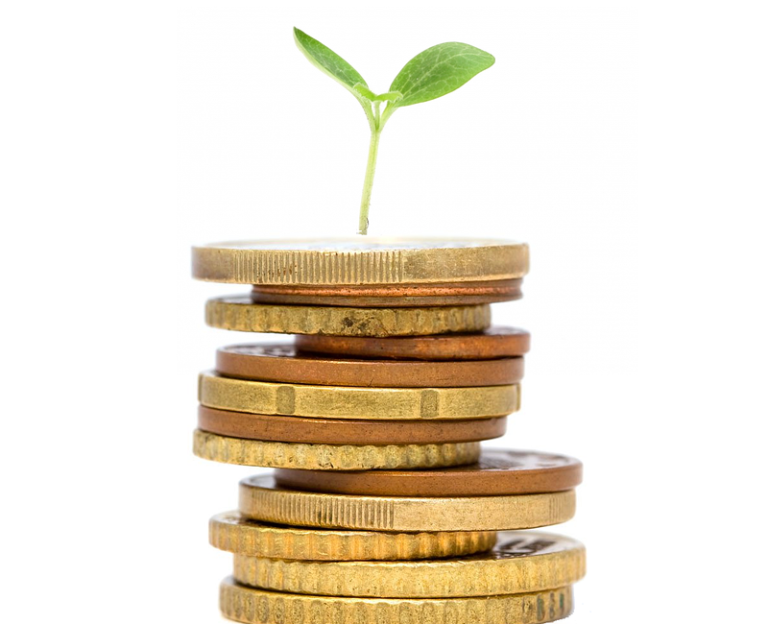
Egy fejlett nesting algoritmussal ellátott és ERP rendszerek felé integrált szoftver alkalmazása egyértelmű versenyelőnyt biztosít a lemezmegmunkáló vállalkozások számára. A legfontosabb előnyök:
Éves szinten több tízezer euró megtakarítás az anyagkihozatal javításával.
Csökkenő CO₂ kibocsátás, amely hosszú távon fenntarthatóbb működést biztosít.
Nagyobb versenyképesség a gyorsabb előkészítés és kisebb gyártási költségek révén.
Aki időben felismeri a fejlett szoftverek nyújtotta lehetőségeket, az jelentős előnyre tehet szert a hazai és nemzetközi piacokon egyaránt. A jövő a hatékonyságról szól!